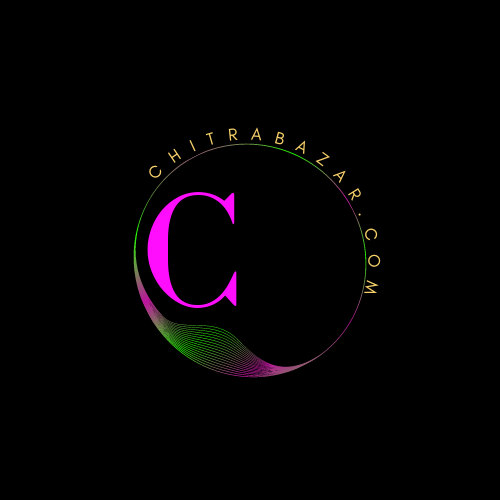
Thought for Today
Believe you can and you're halfway there. - Theodore Roosevelt
CALCINER BURNERS :
Calciners are industrial equipment used in various processes, such as cement production, petroleum refining, and metal smelting, to heat materials to high temperatures. The purpose of a calciner is to thermally decompose or transform raw materials into desired products or intermediate materials. Calciners are commonly used in the production of cement clinker, where they play a crucial role in the calcination process.
- Due to the short residence time in calciners (3 to 4 seconds), combustion can be sensitive to fuel properties. Some fuels such as petcoke – because of its low volatile content, and natural gas – because of its more stringent combustion prerequisites, require more residence time (larger calciner) for satisfactory combustion.
- To understand the operation of a calciner burner, it is important to consider the key parameters involved:
- Air-to-fuel ratio (AFR):
- This is the ratio of the mass flow rate of air to the mass flow rate of fuel. It plays a significant role in the combustion process and affects factors such as flame stability, temperature distribution, and pollutant emissions. The ideal AFR depends on the specific fuel type and the desired process conditions.
- Fuel heating value:
- The heating value of the fuel determines the amount of heat energy released during combustion. It is an essential parameter for calculating the amount of fuel required to achieve the desired heat transfer to the material being processed.
- Burner velocity:
- The velocity at which the fuel and air mixture is injected into the calciner affects the flame stability and heat distribution. Optimal burner velocity ensures proper mixing and combustion of the fuel-air mixture.
- Burner arrangement and geometry:
- The arrangement and geometry of the burner channels or nozzles impact the flow patterns, flame shape, and residence time of the combustion gases within the calciner. These factors influence the heat transfer efficiency and the overall performance of the calciner burner.
- While there are no specific formulas exclusive to calciner burners, the following equations are commonly used to estimate certain parameters and properties related to combustion:
- AFR_s = (W_air / W_fuel)_stoich,
- Where W_air is the mass flow rate of air and W_fuel is the mass flow rate of fuel. The subscript "stoich" denotes the stoichiometric value, which represents the ideal air-to-fuel ratio for complete combustion.
- EAF = (AFR / AFR_s) - 1,
- Where AFR is the actual air-to-fuel ratio used in the calciner burner. The excess air factor indicates the amount of excess air supplied beyond the stoichiometric requirement.
Calciner burners are an integral part of calciners, responsible for providing the necessary heat energy required for the calcination reactions. These burners are designed to efficiently and effectively transfer heat to the material being processed while maintaining the desired temperature and process conditions.
Calciner combustion is quite different from kiln combustion.there is no defined flame in the vessel, with oxidation of the fuel occurring under “flameless” conditions.As for any combustion environment, satisfactory fuel/air mixing is the first requirement for good combustion. Calciner aerodynamics are dominated by the tertiary air due to its mass and comparatively high velocity at the calciner inlet. The airflow patterns can become quite complex with changes in the calciner cross section producing effects such as strong recirculation zones
The design and operation of calciner burners are crucial to achieve optimal calcination results. The primary objective is to ensure uniform and controlled heating of the material. This is typically achieved through the use of specific burner configurations, fuel types, and combustion techniques.
One common type of calciner burner is the multi-channel burner, which consists of multiple small channels or nozzles through which the fuel and air mixture is injected. The fuel can be in the form of natural gas, pulverized coal, or fuel oil, depending on the specific requirements and constraints of the process.
In addition to......
Stoichiometric air-to-fuel ratio (AFR_s):
Excess air factor (EAF):