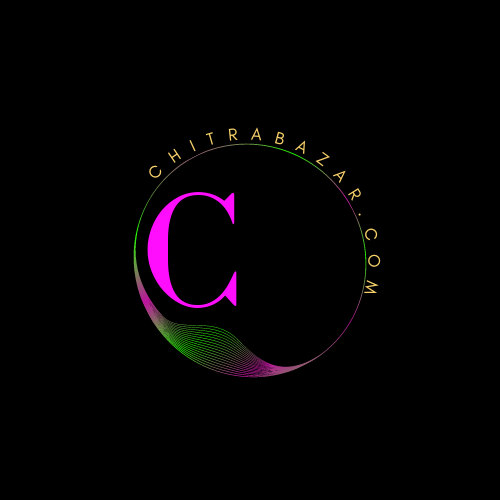
Thought for Today
Happiness is when what you think, what you say, and what you do are in harmony. - Mahatma Gandhi
Importance of Kiln Lining
The kiln lining plays a crucial role in protecting the kiln shell from high temperatures, chemical reactions, and mechanical stresses.
- Types of Kiln Lining Materials:
- Castables:
- Ceramic Fiber:
- Factors Influencing Kiln Lining Selection:
- The temperature range experienced during kiln operation determines the type of refractory material suitable for the lining.
- Chemical Environment:
- The type and composition of materials processed in the kiln, as well as any corrosive or erosive gases present, affect the choice of refractory lining material.
- Mechanical Stresses:
- Proper installation techniques are crucial for the effectiveness and longevity of the kiln lining.
- Kiln Lining Maintenance:
- The installation process involves carefully laying and bonding the refractory bricks or castables using suitable refractory mortars or adhesives.
- Maintenance activities may include repairing or replacing damaged bricks, patching gaps or cracks, and applying protective coatings to enhance the lining's performance and extend its service life.
- Kiln Lining Methods:
- Dry Lining Method:
- In the dry lining method, the refractory bricks or castables are installed without any additional moisture or bonding agents.
- This method is suitable for materials that do not require the formation of chemical bonds between the refractory material and the kiln shell
- Dry lining is commonly used for high-temperature kilns where the operating conditions allow for a dry installation.
- Wet Lining Method:
- The wet lining method involves the addition of water or a bonding agent to the refractory material to create a slurry or mortar.
- The slurry is then applied between the kiln shell and the refractory bricks or castables, allowing it to harden and form chemical bonds.
- Wet lining is often preferred for applications that require a strong and secure bond between the refractory lining and the kiln shell.
- Shotcrete/Gunning Method:
- The shotcrete or gunning method involves spraying or pumping a refractory material, such as a castable or gunning mix, onto the kiln lining surface.
- This method is commonly used for areas that are difficult to access or have complex shapes, allowing for efficient and uniform application of the refractory material.
- Shotcrete/gunning is suitable for both new installations and repairs of existing kiln linings.
- Ceramic Fiber Lining Method:
- Ceramic fiber linings are typically installed using blanket or module systems.
- Ceramic fiber blankets are layered and secured to the kiln shell, providing insulation and protection against heat transfer.
- Module systems consist of pre-formed ceramic fiber modules that are anchored to the kiln shell using hardware.
- The ceramic fiber lining method offers flexibility, easy installation, and excellent thermal insulation properties.
- Bricklaying Method:
- Bricklaying is a traditional method for kiln lining installation, primarily using refractory bricks.
- The bricks are carefully laid and bonded together using refractory mortar or adhesives to form a solid lining.
- This method requires skilled craftsmanship to ensure proper alignment, tight joints, and adequate support for the kiln lining.
Refractory Bricks:
These are commonly used in kiln linings due to their excellent thermal resistance and durability. They are available in various compositions, such as fireclay, high alumina, and silica, depending on the specific application and temperature requirements.
Refractory castables consist of a mixture of refractory aggregates, binders, and additives. They are often used for complex-shaped kilns or areas where brick installation is challenging.
Ceramic fiber linings provide high insulation properties and are commonly used in kilns where energy efficiency is a priority. They are lightweight and have low thermal conductivity.
Operating Temperature:
The mechanical forces experienced by the kiln lining, such as thermal expansion, kiln rotation, and material movement, influence the selection of a suitable lining material with adequate strength and flexibility.
In addition to......
Kiln Lining Installation:
Attention should be given to ensure proper alignment, tight joints, and sufficient thickness of the lining to withstand the thermal and mechanical stresses.
Regular inspection and maintenance of the kiln lining are essential to identify and address any signs of wear, damage, or hot spots.