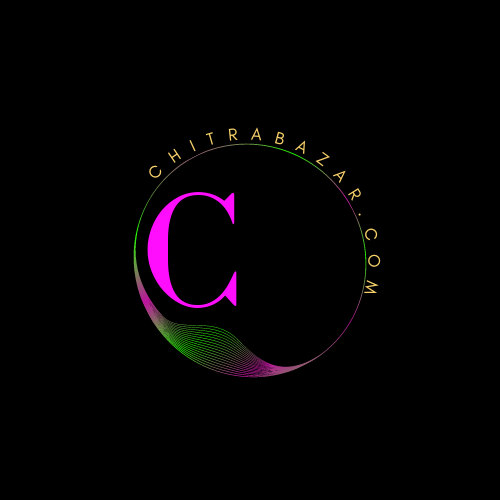
☰
Kiln Burner Design
Kiln burning systems employ different types of burners based on specific requirements and applications. Common types of kiln burners include axial burners, tangential burners, and swirl burners.
- B. Fuel Types and Combustion Techniques
- Solid Fuels:
- Liquid Fuels:
- Combustion Techniques:
- Kiln burners employ various combustion techniques, such as staged combustion, to optimize fuel utilization, reduce emissions, and enhance thermal efficiency. Staged combustion involves injecting fuel and air in multiple stages to control the combustion process and promote complete fuel oxidation.
- C. Burner Placement and Arrangement
- Proper burner placement and arrangement are crucial for achieving uniform heat distribution and efficient combustion in kiln burning systems.
- Multi-Burner Systems:
- Kilns often employ multiple burners distributed along the kiln length to ensure uniform heat transfer. The number and arrangement of burners depend on kiln size, material characteristics, and desired temperature profiles.
- Burner Swirl and Angle:
- Burner swirl and angle play a significant role in flame stability and heat distribution. The swirl motion aids in mixing fuel and air, while the angle determines the flame shape and penetration into the kiln.
- Burner Positioning:
- Burners should be strategically positioned to ensure even heat distribution and minimize hotspots. Factors such as burner spacing, distance from kiln walls, and flame length need to be considered for optimal burner positioning.
- Kiln Burner Optimization:
- Computational fluid dynamics (CFD) simulations and burner optimization techniques can help determine the optimal burner design and placement for efficient combustion, reduced emissions, and improved energy utilization.
- Flame Length Control:
- Controlling the length of the flame is crucial for maintaining the desired temperature profile in the kiln. Adjusting the burner position and flame shape helps achieve the desired flame length and heat distribution.
- Kiln Burner Maintenance:
- Regular maintenance of kiln burners is essential to ensure their optimal performance. This includes cleaning and inspecting the burners, checking for any wear or damage, and replacing worn-out components to maintain efficient combustion.
- Monitoring and Control Systems:
- Installing monitoring and control systems for kiln burners allows for real-time monitoring of key parameters such as flame temperature, fuel-air ratio, and emissions. This data can be used to optimize burner performance and ensure compliance with environmental regulations.
- Burner Retrofits and Upgrades:
- As technology advances, retrofitting or upgrading kiln burners can provide significant improvements in performance, energy efficiency, and emissions reduction. Upgrading to low-NOx burners or incorporating advanced combustion technologies can enhance kiln burner operation.
- Collaboration with Experts:
- Engaging with kiln burner experts and suppliers can provide valuable insights and recommendations for designing and optimizing kiln burners. Their expertise can help in selecting the most suitable burner type, fuel, and combustion techniques for specific kiln requirements.
- Flame Monitoring and Adjustment:
- Regular monitoring of the flame characteristics is essential for kiln burner performance. Flame sensors can be used to measure parameters such as flame shape, length, and temperature. Based on the measurements, adjustments can be made to optimize combustion efficiency and heat distribution.
- Air Distribution Systems:
- Proper air distribution is crucial for efficient combustion in kiln burners. Air distribution systems, such as air registers and windboxes, ensure that the right amount of air is supplied to the burner at the correct velocity and direction. This helps maintain stable flame conditions and uniform heat distribution.
- Burner Cooling and Protection:
- Kiln burners generate high temperatures, and adequate cooling systems are necessary to prevent burner damage and ensure longevity. Water cooling jackets or air cooling systems can be employed to protect the burner components from excessive heat.
- Combustion Air Preheating:
- Preheating the combustion air before it enters the burner can enhance energy efficiency in kiln burning systems. Heat exchangers or recuperators can be installed to recover waste heat from the kiln exhaust gases and use it to preheat the combustion air.
- Computational Modeling and Simulation:
- Computational modeling and simulation techniques, such as computational fluid dynamics (CFD), can be utilized to optimize kiln burner design and placement. These tools help analyze and visualize the flow patterns, heat transfer, and combustion characteristics within the kiln, leading to improved burner performance and energy utilization.
- Environmental Considerations:
- Kiln burner design should also consider environmental factors and emissions regulations. Low-NOx burner designs and emission control technologies can be incorporated to minimize nitrogen oxide emissions and ensure compliance with environmental standards.
- Continuous Improvement and Innovation:
- Kiln burner design is an area of ongoing research and development. Staying updated with the latest advancements in burner technology, such as improved fuel atomization, advanced control algorithms, and alternative fuel utilization, can help optimize kiln burning systems for enhanced performance and sustainability.
Kiln burning systems utilize various fuel types and combustion techniques to achieve optimal performance and efficiency.
Solid fuels like coal, biomass, and alternative solid fuels are commonly used in kiln burning systems. They require proper handling and preparation for efficient combustion.
Liquid fuels such as oil and slurry fuels can be utilized in kiln burners. They offer high energy density and ease of transport, but their combustion characteristics need to be carefully controlled.