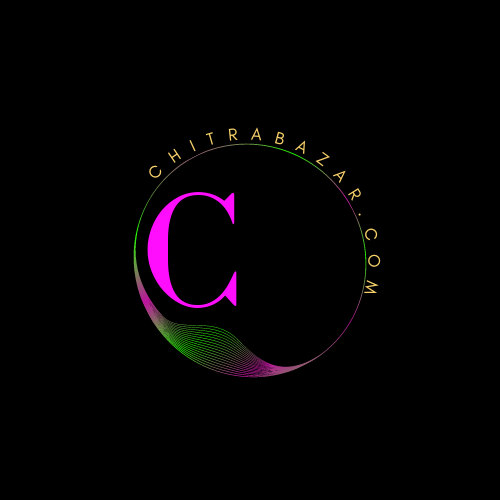
Thought for Today
In three words I can sum up everything I've learned about life: it goes on. - Robert Frost
Kiln Burning Systems: Types, Design, Operation, and Efficiency
Kiln burning systems are critical components in industrial processes such as cement production, where materials are heated to high temperatures to achieve chemical reactions. This section will explain the importance of kiln burning systems in various industries and their role in product quality and process efficiency.
- B. Overview of Kiln Burners and Industrial Furnaces
- II. Types of Kiln Burning Systems
- A. Direct-Fired Kilns
- B. Indirect-Fired Kilns
- C. Semi-Direct-Fired Kilns
- D. Suspension Preheater Kilns
- E. Grate Preheater Kilns
- A. Burner Types
- There are various types of kiln burners available, including axial burners, tangential burners, and swirl burners. This subsection will discuss the characteristics and applications of each burner type.
- B. Fuel Types and Combustion Techniques
- Different fuel types and combustion techniques have an impact on kiln performance and emissions. This section will explore the fuel options and combustion techniques used in kiln burning systems and their effects.
- C. Burner Placement and Arrangement
- The proper placement and arrangement of kiln burners play a crucial role in achieving uniform heat distribution and maximizing fuel efficiency. This subsection will provide guidelines for optimizing burner placement and arrangement.
- A. Startup Procedures
- Proper startup procedures are essential for the safe and efficient operation of kiln burning systems. This section will outline the necessary steps and precautions to be taken during kiln startup.
- B. Operating Parameters and Control
- Maintaining optimal operating parameters and implementing effective control strategies are vital for kiln performance. This subsection will discuss key operating parameters and control techniques for kiln burning systems.
- C. Kiln Inspections and Maintenance Schedule
- Regular inspections and maintenance are necessary to ensure the longevity and reliability of kiln burning systems. This section will provide a recommended inspection and maintenance schedule along with essential maintenance tasks.
- A. Waste Heat Recovery
- Waste heat recovery systems can capture and utilize the excess heat generated by kiln burning systems, leading to improved energy efficiency. This subsection will explore waste heat recovery techniques and their benefits.
- B. Fuel Optimization Strategies
- Implementing fuel optimization strategies can help reduce fuel consumption and operating costs in kiln burning systems. This section will outline various fuel optimization techniques, such as alternate fuel usage and process modifications.
- C. Advanced Control Systems
- Advanced control systems, including predictive control and advanced process monitoring, can enhance energy efficiency and overall performance. This subsection will highlight the advantages and implementation of advanced control systems in kiln burning systems.
- A. Alternative Fuels and Raw Materials
- The use of alternative fuels and raw materials can enhance sustainability and reduce environmental impact in kiln burning systems. This section will discuss the latest innovations in utilizing alternative fuels and raw materials.
- B. Advanced Burner Technologies
- Advanced burner technologies, such as low-NOx burners and flameless combustion, offer improved combustion efficiency and reduced emissions. This subsection will explore the advancements in burner technologies for kiln burning systems.
- C. Digitalization and Automation
- Digitalization and automation have revolutionized kiln technology, enabling better process control and optimization. This section will examine the role of digitalization and automation in enhancing kiln performance and productivity.
One of the most notable aspects of Rajasthan's Kiln burners are devices responsible for supplying and controlling fuel and air flow inside kilns. This subsection will provide an overview of kiln burners, their components, and their interaction with industrial furnaces.
Direct-fired kilns involve the combustion of fuel directly inside the kiln chamber, making them suitable for high-temperature processes. This section will discuss the advantages and applications of direct-fired kilns.
Indirect-fired kilns use external heat sources to transfer heat to the material inside the kiln, making them suitable for processes where direct contact with flames is undesirable. This subsection will explain the principles and benefits of indirect-fired kilns.
Semi-direct-fired kilns combine features of both direct-fired and indirect-fired kilns, providing flexibility in heat transfer mechanisms. This section will describe the characteristics and applications of semi-direct-fired kilns.
Suspension preheater kilns utilize preheating systems to increase energy efficiency and reduce fuel consumption. This subsection will delve into the working principles and advantages of suspension preheater kilns in various industries.
Grate preheater kilns use a series of grates to preheat the material before it enters the kiln, improving thermal efficiency. This section will explain the functioning and benefits of grate preheater kilns.