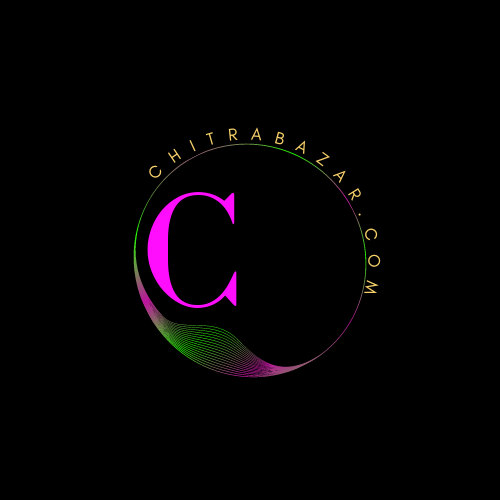
Thought for Today
Your time is limited, don't waste it living someone else's life. - Steve Jobs
Kiln Operation and Maintenance
- Preheating:
- Gradually increase the temperature inside the kiln to remove any moisture and preheat the refractory lining.
- Fuel Ignition:
- Ignite the fuel in the burners following the manufacturer's instructions, ensuring a stable flame is established.
- Ramp-up:
- Gradually increase the kiln's operating temperature while monitoring critical parameters such as fuel-air ratio, flame stability, and exhaust gas temperature.
- System Checks:
- Perform regular checks on instrumentation, safety systems, and control mechanisms to ensure everything is functioning properly.
- Temperature Control:
- Monitor and control the kiln temperature to maintain the desired thermal profile for the specific process. Use temperature sensors and control systems to ensure precise temperature regulation.
- Fuel-Air Ratio:
- Residence Time:
- Kiln Speed:
- Adjust the kiln rotational speed to control the material's advancement through the kiln and maintain the desired residence time.
- Exhaust Gas Analysis:
- Regularly analyze the composition of the exhaust gases to monitor combustion efficiency and emissions. Use gas analyzers to measure parameters such as oxygen, carbon dioxide, and nitrogen oxide levels.
- Regular inspections and maintenance are necessary to ensure the longevity and reliability of kiln burning systems. Follow these guidelines:
- Visual Inspections:
- Lubrication:
- Ensure proper lubrication of bearings, gears, and other moving parts to minimize friction and extend their lifespan.
- Refractory Maintenance:
- Cleaning:
- Regularly clean the kiln internals, including the burner nozzles, flame sensors, and gas passages, to remove any accumulated debris or deposits that can impede proper combustion.
- Maintenance Schedule:
- Establish a comprehensive maintenance schedule that includes routine tasks, such as cleaning, lubrication, and inspection, as well as planned shutdowns for major maintenance activities.
- Safety Checks:
- Prioritize safety checks during inspections to ensure compliance with safety standards and prevent accidents. Inspect safety devices, gas detection systems, and emergency shutdown mechanisms regularly.
- Alignment and Wear:
- Check the alignment of the kiln shell and support rollers to prevent excessive wear and maintain proper kiln operation. Monitor and address any abnormal wear patterns or misalignments promptly.
- Seals and Air Leakage:
- Inspect and maintain the seals between kiln sections and doors to minimize air leakage. Proper sealing helps maintain temperature control and reduces energy loss.
- Preventive Maintenance:
- Implement a proactive preventive maintenance program to address potential issues before they escalate. This includes scheduled inspections, lubrication, and component replacements based on manufacturer recommendations.
- Training and Documentation:
- Ensure that the kiln operators and maintenance personnel receive appropriate training on safe operation, maintenance procedures, and troubleshooting. Maintain comprehensive documentation of maintenance activities and repairs for reference and future analysis.
- Develop and communicate
- Environmental Compliance: Comply with environmental regulations regarding emissions, waste management, and disposal. Install appropriate emission control systems and monitor emissions regularly to ensure compliance.
- Performance Monitoring:
- Implement performance monitoring systems to track kiln efficiency, energy consumption, and production output. Use the collected data to identify areas for improvement and optimize kiln operation.
- Collaboration with Suppliers:
- Establish a strong relationship with kiln equipment suppliers and manufacturers. Consult them for expert advice on maintenance best practices, troubleshooting, and performance optimization.
Achieving the correct fuel-air ratio is crucial for efficient combustion. Use online analyzers and control algorithms to continuously adjust the fuel and air supply to maintain the optimal ratio.
Residence time refers to the duration that the material spends inside the kiln. Proper residence time control ensures complete material calcination and optimal product quality.
C. Kiln Inspections and Maintenance Schedule
Conduct visual inspections of the kiln, burner, refractory lining, and other components to identify signs of wear, damage, or abnormal conditions.
Check the condition of the refractory lining and perform repairs or replacements as needed. Monitor the lining's thickness and integrity to prevent heat loss and ensure efficient heat transfer.