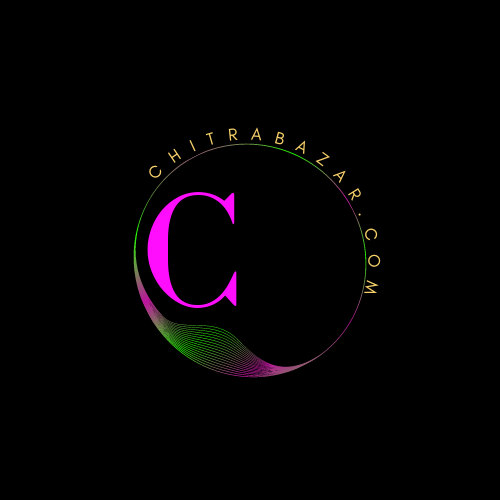
Thought for Today
Happiness is not something ready-made. It comes from your own actions. - Dalai Lama
Kiln Preheating Schedule
Preheating Phase:
Duration: 24 hours
Temperature Range: Ambient to 100°C (212°F)
- Purpose:
- This phase aims to gradually remove any moisture from the kiln and preheat the refractory lining. It prepares the kiln for the subsequent startup process.
- Purpose:
- During this phase, the kiln temperature is gradually increased to a higher range. It allows for further drying of the refractory lining and prepares the kiln for fuel ignition.
- Purpose:
- The soaking phase allows the kiln to stabilize at an intermediate temperature. It helps to ensure uniform heat distribution throughout the kiln and minimizes thermal stress on the refractory lining.
- Purpose:
- In this phase, the kiln temperature is increased from the soaking temperature to the desired operating temperature. It allows for the complete drying of the refractory lining and prepares the kiln for production.
- Soak and Stabilization Phase:
- Purpose:
- During this phase, the kiln is held at the desired operating temperature to ensure complete stabilization of the refractory lining and other kiln components. This helps optimize heat distribution and prepares the kiln for production.
- Preheating Monitoring:
- Regularly check and record the temperature readings to ensure that the preheating schedule is progressing as planned.
- Safety Considerations:
- Ensure proper ventilation during the preheating process to remove any gases or fumes released during the heating of refractory materials.
- Follow safety protocols and wear appropriate personal protective equipment (PPE) when working around the kiln during the preheating phase.
- Keep a safe distance from the kiln during the preheating process and avoid any direct contact with hot surfaces.
- Preheating Checklist:
- Before starting the preheating process, ensure that all kiln doors and access points are closed properly.
- Verify that the kiln's ventilation system is functioning correctly and that air circulation is adequate.
- Inspect the burners and ensure that they are clean and in good working condition.
- Check the temperature sensors for accuracy and proper functioning.
- Monitor the preheating process closely, keeping a log of temperature readings and any observations or abnormalities.
- Cooling Phase:
- Duration: After the preheating process is complete, allow the kiln to cool gradually to ambient temperature before further operations or maintenance activities.
- Purpose:
- The cooling phase helps prevent thermal shock and potential damage to the refractory lining and other kiln components. It allows for safe access to the kiln for inspection, maintenance, or loading/unloading of materials.
- Post-Preheating Inspections:
Ramp-up Phase:
Duration: 12 hours
Temperature Range: 100°C (212°F) to 500°C (932°F)
Soaking Phase:
Duration: 4 hours
Temperature Range: 500°C (932°F) to 800°C (1472°F)
Final Ramp-up Phase:
Duration: 8 hours
Temperature Range: 800°C (1472°F) to the desired operating temperature
In addition to......
Duration: 2 hours
Temperature Range: Desired operating temperature to allow the kiln to stabilize
Use temperature sensors strategically placed within the kiln to monitor the temperature during the preheating process.
Adjust the preheating duration or temperature ranges if necessary based on the monitored data and any specific requirements of the materials being processed.