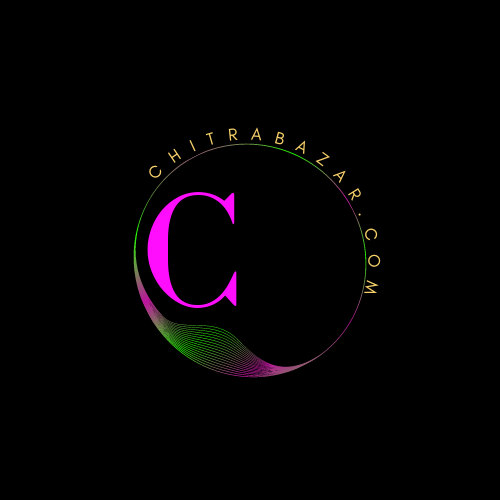
☰
Thought for Today
Strength does not come from physical capacity. It comes from an indomitable will. - Mahatma Gandhi
Troubleshooting and Problem Solving
Effective troubleshooting techniques can help identify and resolve issues in kiln operation. Consider the following steps:
- Identify the Problem:
- Clearly define the problem by observing and analyzing the symptoms, such as abnormal temperature readings, fluctuating flame, or poor product quality.
- Root Cause Analysis:
- Conduct a root cause analysis to determine the underlying factors contributing to the problem. This may involve inspecting equipment, reviewing operating parameters, and analyzing process data.
- Data Collection:
- Gather relevant data, including temperature readings, combustion parameters, and process variables, to aid in troubleshooting and problem solving.
- Collaboration and Expert Assistance:
- Engage with kiln experts, equipment suppliers, and colleagues to seek their insights and expertise in diagnosing and resolving complex issues.
- Systematic Approach:
- Follow a systematic approach to problem solving, using tools such as the PDCA (Plan-Do-Check-Act) cycle or the 5 Whys technique to identify potential solutions and implement corrective actions.
- Proper training and knowledge transfer are essential for effective kiln operation and maintenance. Consider the following aspects:
- Operator Training:
- Provide comprehensive training programs for kiln operators, covering topics such as safety protocols, operating procedures, parameter control, and emergency response.
- Maintenance Training:
- Equip maintenance personnel with the necessary skills and knowledge to perform routine maintenance tasks, troubleshooting, and equipment repairs.
- Knowledge Management:
- Establish a knowledge management system to capture and document operational expertise, lessons learned, and best practices. This facilitates knowledge transfer between personnel and ensures continuity of knowledge.
- Continuous Learning:
- Encourage a culture of continuous learning and professional development among kiln operators and maintenance staff. Stay updated with industry advancements, attend seminars, and participate in training programs to enhance skills and knowledge.
- Standard Operating Procedures:
- Develop and regularly update standard operating procedures (SOPs) for kiln operation, maintenance, and troubleshooting. SOPs provide clear guidelines and ensure consistent practices.
- Optimizing energy efficiency in kiln operation can lead to cost savings and reduced environmental impact. Consider the following measures:
- Heat Recovery Systems:
- Install heat recovery systems, such as waste heat boilers or heat exchangers, to capture and utilize waste heat from kiln exhaust gases for various purposes, such as preheating combustion air or generating steam.
- Insulation:
- Improve insulation on the kiln shell and related equipment to minimize heat loss. Proper insulation reduces energy consumption and helps maintain stable operating temperatures.
- Alternative Fuels:
- Explore the use of alternative fuels, such as biomass or waste-derived fuels, as a substitute for conventional fossil fuels. Proper handling and combustion of alternative fuels can reduce energy costs and carbon emissions.
- Process Optimization:
- Continuously evaluate and optimize the kiln process parameters, such as airflow, material feed rate, and flame characteristics, to achieve maximum efficiency and minimize energy waste.
- Kiln Scheduling:
- Plan kiln operation and material loading to optimize energy consumption. Consider factors such as production demand, material characteristics, and kiln thermal inertia to achieve efficient and balanced kiln utilization.
- Personal Protective Equipment (PPE):
- Ensure that all personnel working around the kiln wear appropriate PPE, including heat-resistant clothing, safety glasses, gloves, and hearing protection.
- Lockout/Tagout Procedures:
- Implement lockout/tagout procedures to safely isolate and de-energize the kiln and associated equipment during maintenance and repair activities.
- Fire Safety:
- Have adequate fire detection and suppression systems in place. Conduct regular fire drills, ensure the availability of fire extinguishers, and train personnel in fire safety protocols.
- Ventilation:
- Maintain proper ventilation in the kiln area to control emissions, remove hazardous gases, and ensure a safe working environment.
- Emergency Response:
- Establish clear emergency response protocols and communication channels for handling kiln-related emergencies. Train personnel in emergency procedures, evacuation plans, and first aid.
Training and Knowledge Transfer
Energy Efficiency and Optimization
Safety Considerations
Safety is of paramount importance in kiln operation and maintenance. Consider the following safety considerations: